Electrical Power and Transmission
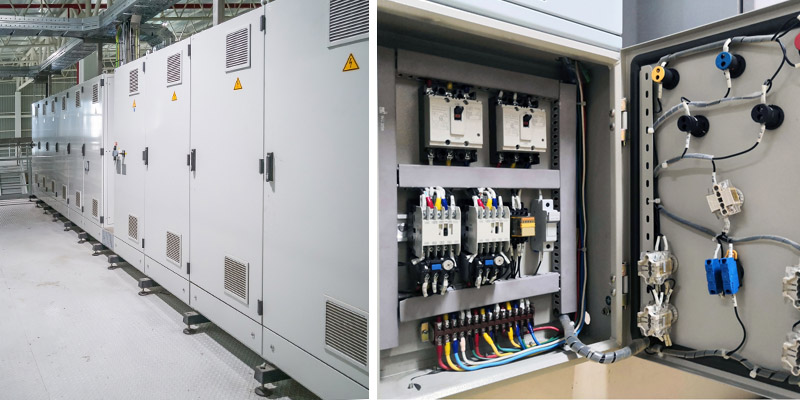
Anodizing in Electrical Engineering
In electrical engineering, anodizing plays a crucial role in enhancing the durability and performance of various components. Take, for instance, electrical enclosures and control panels, which are often anodized to ensure long-term corrosion resistance. The anodized layer acts as a protective barrier, safeguarding these critical components against environmental factors and maintaining electrical integrity.
Additionally, anodizing is extensively utilized in the production of heat sinks. The enhanced thermal conductivity of anodized aluminium allows for efficient heat dissipation, crucial for electronic devices that generate heat during operation. This is particularly beneficial in power electronic systems where effective heat management is vital for optimal performance and longevity.
Another notable application is in anodized aluminium wiring. The anodized layer provides an extra level of protection against corrosion, ensuring the reliability of electrical connections over time. This is especially important in environments where exposure to moisture or harsh chemicals is a concern.
Beyond these examples, anodizing is also employed in the manufacturing of connectors, terminals, and bus bars. The corrosion resistance offered by anodized surfaces ensures consistent and reliable electrical conductivity, contributing to the overall efficiency and safety of electrical systems.
Anodize Printing in the Electrical World
In the realm of electrical engineering, anodize printing serves as a versatile solution for labelling and marking various components, providing clear identification and information. In a large-scale power plant, anodize printing is utilized on control panels, indicating critical functions, safety instructions, and system specifications. This not only ensures efficient operation but also enhances the overall safety of the facility.
In a smaller substation facility, anodize printing finds application on circuit breakers, transformers, and switchgear components. Clear and durable markings on these vital components aid in quick and accurate identification during routine inspections or in emergency situations, facilitating efficient maintenance and troubleshooting processes.
Moreover, anodize printing extends its utility to various locations within the electrical infrastructure. For instance, utility poles may be marked with anodized labels to indicate voltage levels and other essential information for maintenance crews. In data centres, anodize printing on server racks provides clear identification of equipment and ensures streamlined cable management.
In both large-scale power plants and smaller substations, anodize printing contributes to maintaining a well-organized and efficient electrical infrastructure. The clarity, durability, and adaptability of anodize printing make it an invaluable tool for enhancing safety, reliability, and overall functionality in diverse electrical engineering applications.